Glossar
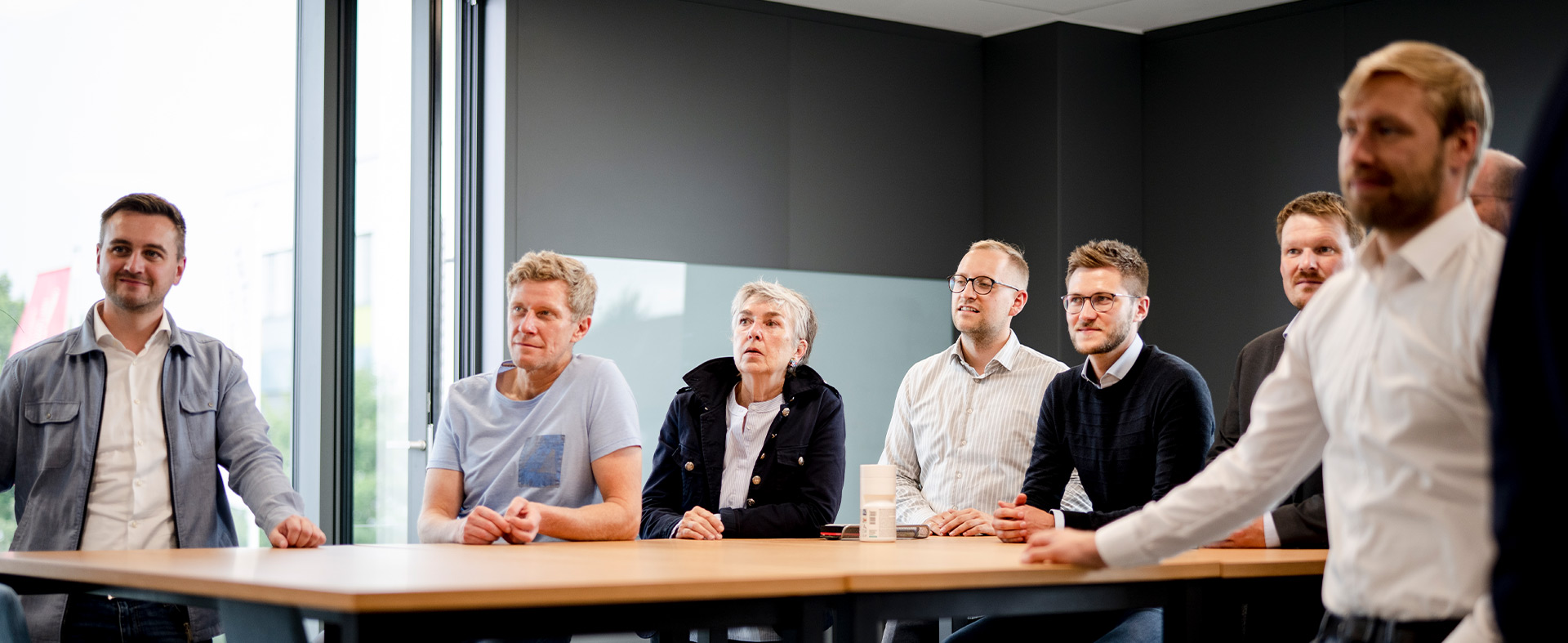
Glossar A - Z
Im Glossar finden Sie wichtige Begriffe und Methoden, die uns in unserer täglichen Arbeit begleiten.
A |
B |
C |
D |
E |
F |
G |
H |
I |
J |
K |
L |
M |
N |
O |
P |
Q |
R |
S |
T |
U |
V |
W |
X |
Y |
Z |
0-9 |
Größere Anzahl von Elementen (produzierte Artikel, Material, Lagerware, ...), die nach bestimmten Kriterien (Häufigkeit, Stückzahlen, Umsatz, ...) geordnet und entsprechend A- (sehr wichtigen), B- (wichtigen) und C- (weniger wichtigen) Segmenten klassifiziert werden
Auch als Arbeitsablaufschema, Operationsfolgediagramm oder Ablaufdarstellung bezeichnet, um Struktur, Bestandteile und Daten eines Ablaufs über mehrere Arbeitssysteme zu erfassen und darzustellen. Hier dient das Ablaufschema dazu, übersichtlich zu zeigen, wie mehrere Teile bzw. Baugruppen einzelne Arbeitssysteme durchlaufen
Untersuchung der Altersstruktur von Mitarbeitern eines Unternehmens oder Unternehmensbereichs, um auf dieser Basis mögliche künftige Personalprobleme zu identifizieren und Maßnahmen (z. B. Neueinstellungen oder Qualifizierungen) zu initiieren
Ermittlung von Zeiträumen, in denen aus den Rückflüssen von Investitionsvarianten die durch sie verursachten Anschaffungskosten gedeckt werden. Diese Zeiträume werden als Amortisations- oder Wiedergewinnungszeiten bezeichnet. Die Amortisationsrechnung kann eingesetzt werden, um Investitionsvarianten in Bezug auf die Zeitspannen des Kapitalrückflusses zu beurteilen. Zudem können Einzelinvestitionen darauf hin überprüft werden, ob sie sich innerhalb einer vorgegebenen Zeitspanne ‘amortisieren’
Datenaufnahme (Messen, Beobachten, Beschreiben) sowie Bewerten einer Ausgangssituation
Methode, mit der Arbeitssysteme so zueinander angeordnet werden können, dass der Transportaufwand minimal ist
Modell für eine betriebliche Leistungseinheit, die eine Person/mehrere Personen, notwendige Betriebsmittel, Material/Informationen sowie die dabei bestehenden Bedingungen erfasst. Ein Arbeitssytem kann – je nach Abgrenzung – sowohl Arbeitsplätze, Produktionsbereiche oder eine gesamte Fabrik umfassen
Strukturierung von Unternehmen in Funktionen (z. B. Bereiche oder Abteilungen), um deren Zusammenarbeit, Ausstattung und Zuständigkeiten darzustellen. In der Regel wird die Aufbauorganisation in Form von sog. Organigrammen visualisiert
Methode, mit der vor allem die Unterstützungsprozesse aufgenommen und bewertet werden können (z. B. nach Personalaufwand, Zeit, Beständen oder Qualität)
Ziel- und Führungssystem, das neben der finanziellen Dimension auch die Dimensionen Markt und Kunden, Produkte, (interne) Prozesse sowie Mitarbeiter und Führung berücksichtigt. Die Dimensionen können reduziert oder ergänzt werden. Das System ist durchgängig von der Vision über Unternehmensgrundsätze, Unternehmens-/, Bereichs-/Abteilungs- bis hin zu Gruppenzielen angelegt. Es verknüpft die strategische mit der operativen Führung und ist daher für alle Mitarbeiter nachvollziehbar
Externe Einflussfaktoren, die durch ein Unternehmen nicht beeinflussbar sind, wie volkswirtschaftliche Veränderungen, neue Wettbewerber oder ‘Wegbrechen’ von Märkten sowie interne Einflussfaktoren, die durch ein Unternehmen beeinflussbar sind, wie ein überalterter Maschinenpark, lange Transportwege oder Qualifikationsdefizite
Kontinuierliches Messen von Zielgrößen, z. B. in Bezug auf Produkte, Dienstleistungen, Gestaltungsmaßnahmen und Vorgehensweisen. Anliegen ist es, die eigene Leistung möglichst mit dem besten Unternehmen vergleichen zu können und sich permanent zu verbessern.
Benchmarks sind in diesem Zusammenhang festgelegte Bezugswerte (z. B. Branchendurchschnittswerte oder Werte des besten Unternehmens im Wettbewerb)
Methode, um für Optimierungsprojekte – besonders der Ebenen Fabrik oder Produktionsbereich – die Gebäudestruktur, das wesentliche Inventar sowie die Flächen und deren Nutzung aufzunehmen
Beinhalten Anlagen, Maschinen, Werkzeuge, Organisationsmittel, Möbel und sonstige Geräte, die in einem Arbeitssystem direkt oder indirekt mitwirken, um eine Arbeitsaufgabe auszuführen. Manchmal wird zwischen Betriebs- und Arbeitsmitteln unterschieden. Dann sind Betriebsmittel der Produktion und Arbeitsmittel dem administrativen Bereich zuzuordnen
Nicht oder nur schwer monetär quantifizierbare Zielgrößen im Rahmen einer Nutzwertanalyse, wie z. B. Übersichtlichkeit in einer Produktionshalle, Kreuzungsfreiheit von Materialflüssen oder Erweiterungsfähigkeit von Produktionsbereichen
Wird im frühen Planungsstadium eingesetzt, um Arbeitsplätze als Kartonagen-Modelle im Maßstab 1:1 entwickeln. Betroffene Mitarbeiter werden dabei aktiv in die Planung einbezogen, indem sie ihren eigenen Arbeitsplatz mit einfachst zu bearbeitenden Materialien, wie Kartonage, Dachlatten, Styropor, Schaumstoff oder Klebeband aufbauen und optimieren. Hauptvorteile der Methode sind eine hohe Akzeptanz für die Arbeitsplatzgestaltung bei den Betroffenen sowie das Vermeiden von Fehlplanungen oder kostenintensiven Modifikationen
Checkliste zur Berücksichtigung der wesentlichen wirtschaftlichen und ergonomischen Anforderungen in der Phase der Neuplanung von Arbeitsplätzen sowie für die Optimierung existierender Arbeitsplätze. Sie wird unterteilt in die Bereiche Werkzeug/Vorrichtung/Hilfsmittel, Materialbereitstellung, Arbeitsmethode, Körperhaltung/Arbeitshöhe, Arbeitssicherheit/Arbeitsumgebung und Tätigkeit
Checkliste, um sich zu Beginn von Planungs- und Optimierungsprojekten schnell einen Überblick zu den wesentlichen ‘Eckpunkten’ eines Unternehmens zu verschaffen und um mit Basiszahlen Effekte von Verbesserungen monetär bewerten zu können
Checkliste, mit der die typischen Erfolgsfaktoren für Veränderungsprojekte berücksichtigt werden können, wie Projektorganisation, Veränderungstempo, Projektleitung, Beratung, gemeinsame Ziele im Management, Vision, Personalentwicklung, Feedback, ganzheitliches Denken und Handeln, Kommunikation, Partizipation, Führung, Schlüsselpersonen, Emotionen und Widerstand
Checkliste, um Hinweise zur Vermeidung unbeabsichtigter Fehler bei menschlicher Arbeit zu erhalten. Mit Poka Yoke (zufällige Fehler vermeiden) soll durch einfachste, aber sehr wirkungsvolle technische und organisatorische Hilfsmittel Fehlverhalten im Produktionsprozess sofort unterbunden werden. Die Checkliste Fehlervermeidung fragt die Aspekte Verwechslen, nicht exaktes Fügen und Vergessen ab
Checkliste, um zu Beginn der Durchführung einer Groblayouplanung die wesentlichen Layout-Einflussfaktoren zu berücksichtigen. Diese werden untergliedert in Flächenbedarf, Grundstück, Gebäude, Material-/Energie-/Personenfluss, Fertigungsprinzipien und Produktion
Checklisten mit Anforderungen an eine Unternehmensvision und die daraus abgeleiteten Unternehmensgrundsätze
Checkliste mit Aspekten, wie Farbkonzept, Informationsbereitstellung sowie Visualisierung in der Logistik oder in Arbeitssysstemen. Visuelles Management dient dazu, Informationen über Arbeitsabläufe und -ergebnisse so transparent zur Verfügung zu stellen, dass jeder sofort erkennen kann, ob es sich um einen normalen Prozesszustand ober eine Abweichung handelt.
Methode, um zu Beginn von Prozessoptimierungsprojekten geeignete Zielgrößen, Kennzahlen sowie Messgrößen zu definieren und um den Erfolg von Optimierungsmaßnahmen nach der Umsetzung überprüfen zu können. Zudem unterstützt die Checkliste Ziele den Prozess der Erarbeitung einer Balanced Scorecard (BSC). Die Zielgrößen orientieren sich an den Dimensionen einer BSC
Daten vor Ort durch Beobachten, Messen und Befragen aufnehmen. Vorteil: Aktualität; Nachteile: nur Augenblicksaufnahme/oft Störung des Betriebsablaufs
Betriebliche Funktionen in Geschäfts-/Kernprozessen, die der unmittelbaren Wertschöpfung dienen (z. B. Fertigung, Montage)
Tätigkeiten, die der unmittelbaren Wertschöpfung dienen, wie Fertigen oder Montieren
Struktur, die folgende Gestaltungshierarchie beinhaltet: Unternehmenführung > indirekter Bereich > Fabrik > Produktionsbereich > Arbeitsplatz. Sie folgt der Logik ‘vom Umfassenden zum Detail’
Untersuchung der unternehmensinternen beeinflussbaren Bedingungen, wie technische Ausstattung, interne Prozesse, Führungsverhalten oder Mitarbeiterqualifikation (vgl. auch Stärken und Schwächen in der SWOT-Analyse)
Methode zur Detaillierung eines Groblayouts. Hier fließen weitere, über das Groblayout hinausgehende, bislang noch nicht berücksichtigte Layout-Einflussfaktoren und Ziele ein. Die einzelnen Flächenelemente eines Groblayouts werden nun beispielsweise mit Maschinen-, Arbeitsplatz-, Lagerskizzen, Materialbereitstellflächen, Stichwegen und sonstigen Stellplätzen (für Schränke, Besprechungsbereiche usw.) detailliert dargestellt. Ergebnis ist ein Layout, in dem möglichst sämtliche Planungsziele und Layout-Einflussgrößen berücksichtigt sind und das sich zum Aufbau einer Produktion eignet
Punkt-, Werkstatt-, Gruppen-/Linien- oder Fließfertigung
Prinzip, nach dem Teile des Vorgängerprozesses auf FIFO-Bahnen gelegt werden (z. B. Rollenbahn, Förderband, Rutsche). Die Abarbeitung erfolgt im Nachfolgeprozess in gleicher Reihenfolge (First-In-First-Out)
Ermittlung von Maschinenarbeits-, Bereitstellflächen, Flächen für Stichwege und sonstigen Flächen im Bereich der Arbeitssysteme sowie der Hauptwege, um damit die Produktionsfläche zu erhalten. Dies kann rechnerisch auf Basis der Maschinen- und Arbeitsplatzgrundflächen geschehen oder durch Abschätzung mit Kennzahlen
Methode, um einen visuellen Vorher-Nachher-Vergleich zu ermöglichen, etwa im Rahmen der Gestaltung von Arbeitssystemen. Zudem wird die Methode zur Dokumentation von Workshopergebnissen eingesetzt
Methode, in der verschiedene Maßnahmen und deren realisierbare Potenziale in einer Auflistung übersichtlich dargestellt und summiert werden (z. B. im Rahmen einer Potenzialstudie). Diese Liste dient zugleich der Projektsteuerung, indem der Umsetzungsstand der definierten Projekte laufend dokumentiert wird
Prozesse, auch Kernprozesse genannt, in denen ein Kundennutzen erzeugt wird. Ausgangs- und Endpunkt ist der Kunde. In Geschäftsprozessen agieren i. d. R. direkte Funktionsbereiche, in denen direkte Tätigkeiten erfolgen. Den Geschäftsprozessen lassen sich die Ebenen Fabrik, Produktionsbereiche und Arbeitsplätze zuzuordnen
Um- und Durchsetzung von Maßnahmen (technisch, organisatorisch, personell) zur Lösung festgestellter Probleme
Sammelbegriff, beispielsweise für Standardisierung, kontinuierlichen Verbesserungsprozess oder visuelles Management, denen ein ‘Methodenbaukasten’ mit einheitlicher Ausrichtung zugeordnet werden kann
Methode, um Erlöse in die Wirtschaftlichkeitsrechnung einzubeziehen (Gewinn = Kosten - Erlöse). Damit erhöht sich die Aussagekraft der Wirtschaftlichkeitsrechnung. Die Gewinnvergleichsrechnung kommt zur Anwendung, wenn die Vorteilhaftigkeit verschiedener Investitionsvarianten zu beurteilen oder ein einzelnes Investitionsobjekt darauf hin zu überprüfen ist, ob es Gewinn erzielt
Erzeugen eines Reallayouts als Vorstufe zur dataillierteren Feinlayoutplanung. Es ist eine grundrissgeometrische Darstellung unter Berücksichtigung der wesentlichen Layout-Einflussfaktoren. Ein Groblayout wird immer ein Kompromiss aus Ideallayout und den real verfügbaren Raum- und Flächenstrukturen sein. Der Detaillierungsgrad eines Groblayouts kann sehr unterschiedlich sein, sollte jedoch Stützenraster, Hauptwege, Hallentore sowie Arbeitssysteme in ihrer groben Form enthalten. Zum Teil können auch bereits Stichwege eingezeichnet werden
Organisationsform, in der Arbeitsgruppen mit einer überschaubaren Anzahl an Mitarbeitern gebildet werden. Diese Gruppen übernehmen nach und nach Tätigkeiten aus Unterstützungsprozessen (indirekte Tätigkeiten) sowie Tätigkeiten aus Führungsprozessen (Tätigkeiten der Selbststeuerung) und erhalten somit einen stetig steigenden Autonomiegrad
Methode, um mitttels Ausgleichskästen oder Plantafeln verschiedene zu fertigende Produkte (Varianten) gleichmäßig über einen definierten Zeitraum zu verteilen. Dadurch werden eine hohe Reaktionsfähigkeit auf schwankende Kundenanforderungen sowie reduzierte Bestände und Durchlaufzeiten gewährleistet
Kopplung der beiden wesentlichen Aspekte ‘Produktivität’ und ‘Humanorientierung’ für den Unternehmenserfolg, auch als ‘Humanorientiertes Produktivitätsmanagement’ bezeichnet
Basis für eine (flächenmaßstäbliche) Groblayoutplanung. Zudem kann später die Qualität von Groblayouts überprüft werden, indem ein Vergleich mit den Ideallayouts erfolgt. Ideallayouts werden auf Basis der Anordnungsoptimierung/Ideallayout-Skizzen erstellt und unterliegen – mit Ausnahme der ermittelten Flächenbedarfe – keinen Restriktionen
Erste Skizze für ein nach Materialflussgesichtspunkten optimiertes Layout ohne Berücksichtigung von Arbeitssystem-Dimensionen. Sie ergibt sich aus der Methode Anordnungsoptimierung und dient als Basis für ein Ideallayout
Erfassen von Daten aus vorhandenen Unterlagen. Vorteile: repräsentativer Betrachtungszeitraum, keine Störung des Betriebsablaufs; Nachteil: meist nicht aktuell
Alle Unternehmensfunktionen, die nicht direkt der Produktion zugeordnet werden, wie z. B. Vertrieb, F&E/Konstruktion, Arbeitsvorbereitung oder Einkauf. Sie bereiten einen Kundenauftrag vor, planen und steuern ihn. In diesen Funktionen sind die unterstützenden Prozesse zu verorten, wie z. B. der Auftragsdurchlauf
Tätigkeiten zur unmittelbaren Unterstützung der wertschöpfenden Tätigkeiten, wie Auftragsfeinplanung, Qualitätssicherung oder Materialbereitstellung
An zentralen Stellen des Unternehmens aufgestellte Tafeln/Wände, auf denen sämtliche wesentlichen Informationen in verständlicher und gut lesbarer Form kommuniziert werden (z. B. allgemeine Informationen zum Unternehmen, Bereichssziele, KVP-Aktivitäten, Gestaltungsmaßnahmen). Die Informationswände werden ständig aktualisiert
Vorstufe für eine quantitative Potenzialanalyse, um zwei Bereiche zu untersuchen: 1) Niveau der Arbeitsgestaltung: Dadurch lässt sich erkennen, welche Gestaltungsmaßnahmen in einem Produktionsunternehmen – orientiert an sogenannten Gestaltungsfeldern – umgesetzt worden sind. 2) Niveau des Einsatzes von Prozessoptimierungsmethoden: Durch eine systematische Analyse der eingesetzten Methoden kann ein Rückschluss auf die ‘Methodendurchdringung’ im Unternehmen und damit i. d. R. auf das vorhandene Qualifikationsniveau gezogen werden
Pull-Steuerung (ziehende Steuerung) durch ‘Karten’. Einfachste Version: An jedem Teil befindet sich eine Produktions-Karte (Produktions-Kanban) mit wichtigen Informationen für den Zulieferprozess. Bei einer Teileentnahme durch den Nachfolgeprozess wird die Produktions-Karte an den Vorgängerprozess zur Nachproduktion geschickt
Prozess, der durch die aktive Beteiligung einer Gruppe von Mitarbeitern an der Optimierung ihrer Arbeitsbedingungen gekennzeichnet ist. Hier stehen stetiges Erkennen und sofortiges Umsetzen von Verbesserungen mit geringsten Investitionen und ohne Bürokratie im Vordergrund
Verwendung, wenn mehrere funktionsgleiche/-ähnliche Investitionsvarianten miteinander zu vergleichen sind, um die vorteilhafteste zu bestimmen (Gesamtkosten von Variante 1 vs. Gesamtkosten von Variante 2) oder wenn eine Ersatzinvestition erfolgen soll (Gesamtkosten vor der Investition vs. Gesamtkosten nach der Investition). Die Erlöse bleiben unberücksichtigt
Verhältnis aus verfügbarer Betriebszeit pro Periode und Kundenbedarf pro Periode. Er ist der ‘Herzschlag’ für einen Wertstrom
Flankieren die Unterstützungs- und Geschäfts-/Kernprozesse, können diese aber auch auslösen, z. B. Neuentwicklungsvorhaben
Methode zur Ermittlung von Transportkosten zwischen bestehenden Arbeitssystemen oder für geplante Layoutvarianten. Zu den Materialflussprozessen zählen das Transportieren sowie Handhaben und Lagern von Arbeitsgegenständen; für die Materialflussanalyse wird hier jedoch ausschließlich der Prozess des Transportierens untersucht. Wesentliche Schritte der Methode sind: Erstellen einer Transportmatrix, eines Sankey-Diagramms und einer Wegematrix sowie die Berechnung des Mengen-Wege-Produkts
Mathematisches Produkt aus Transporthäufigkeit pro Zeiteinheit (Anzahl Transporte/Jahr) und Weg (Entfernungen im m) zwischen zwei Arbeitssystemen. Multipiziert man dieses mathematische Produkt mit einem Kostenfaktor für einen Transportmeter (z. B. 0,038 €/m), erhält man die Gesamttransportkosten pro Jahr zwischen zwei Arbeitssystemen
Methode zur Berechnung des Mengen-Wege-Produktes. Dazu werden die Werte aus der Transportmatrix mit den korrespondierenden aus der Wegematrix multipliziert. Abschließend werden alle Werte in dieser Matrix summiert (Summe Transportmeter pro Jahr). Multipiziert man diese Summe mit einem Kostenfaktor für einen Transportmeter (z. B. 0,038 €/m), erhält man die Gesamttransportkosten pro Jahr für ein Layout
Moderationsmethode mittels beschreibbarer farbiger Karten, die an Pinnwände geheftet und strukturiert werden. Die Vorteile dieser Methode liegen vor allem darin, dass alle Teilnehmenden in die Erarbeitung von Ergebnissen aktiv miteinbezogen werden
Standardisierte Vorgehensweise, die meist einem Gestaltungsprinzip zugeordnet werden kann, wie z. B. die Methode 5S dem Gestaltungsprinzip Standardisierung. Methoden helfen somit Unternehmensziele zu erreichen
Material mit bekanntem (kontinuierlichem) Verbrauch wird, in Anlehnung an das amerikanische Milchmann-Prinzip, turnusmäßig an definierten Bereitstellplätzen in der Produktion angeliefert. Leergut wird auf dem Rückweg sofort mitgenommen. Damit lässt sich eine kontinuierliche Materialversorgung bei verringertem Transportaufwand sicherstellen
MTM (Methods Time Measurement) gehört zu den Systemen vorbestimmter Zeiten. MTM-1 wird für sehr detaillierte Analysen mit 19 Grundbewegungen (Einsatz für die Massenfertigung) verwendet, UAS (Universelles Analysiersystem) für ‘gröbere’, dafür aber schnellere Analysen mit 7 Grundvorgängen (Einsatz für die Serienfertigung). MTM lässt sich bereits in den Phasen ‘Produktkonzeption’, ‘Produktentwicklung’, ‘Konstruktion’ und ‘Produkterprobung’ im Produktentwicklungsprozess einsetzen. Im Fokus von MTM stehen die Ermittlung von Fertigungszeiten sowie die Montageoptimierung durch Eliminieren nicht wertschöpfender Tätigkeiten, insbes. schwieriges Handhaben von Teilen oder kompliziertes Fügen
Methode zur Erfassung der Häufigkeit von Ereignissen/Ablaufarten in Arbeitssystemen, die zu festgelegten Zeitpunkten während Rundgängen festgehalten werden. Damit können z. B. untersucht werden: Betriebsmittelnutzungsgrade, auftretende Störungen oder Verschwendungsanteile
Planung auf der ‘grünen Wiese’ (Neubau, Umzug, Verlagerung) ohne gravierende Planungseinschränkungen
Punktwert- oder Scoringverfahren zur Bewertung nicht oder schwer monetär bewertbarer Kriterien. Entscheidungsträger können mit vergleichsweise geringem Aufwand ihre Präferenzen systematisch in einen Entscheidungsprozess einbringen. Ergebnis ist der sog. Gesamtnutzwert für Lösungsalternativen. Die Variante mit dem höchsten Gesamtnutzwert erfüllt dabei am besten die Ziele
Prinzip, mit dem im Idealfall jedes Teil einzeln von einem zum nächsten Prozess weiter transportiert und bearbeitet wird. Realistisch ist, dass Teile in kleinsten Losen (Batches) weitergeschoben werden
Aufteilung von Fertigungslosen in ‘Packeinheiten’ und zielgerichtet auf verfügbare Ressourcen (Pitches = gleichgroße Produktionsvolumina). Pitches dienen dazu, Kunden auch mit kleinen Stückzahlen wirtschaftlich zu bedienen, einen gleichmäßigen ‘Herzschlag’ im Gesamtprozess zu realisieren, auf Änderungen optimal reagieren zu können und geringste Bestände im Gesamtprozess zu haben
Methode zur groben orientierenden Erfassung von Optimierungspotenzialen. Hier steht im Vordergrund, schnell und aufwandsarm erste Hinweise zu Optimierungspotenzialen zu erhalten
Neu- bzw. Weiterentwicklung von Produkten, um dadurch einen Wettbewerbsvorteil zu erlangen
Fertigung (i. d. R. mechanische Fertigung) und Montage (Zusammenbau der vorgefertigten Teile)
Prozessoptimierungen – auch als Prozessinnovationen oder -verbesserungen bezeichnet –, die sich auf unternehmensinterne Strukturen mit dem Fokus auf Arbeitsproduktivität, Durchlaufzeiten, Bestände, Betriebsmitteleffektivität, Ergonomie usw. beziehen. Sie sind dringend notwendig, um beispielsweise mit den erzielten Effekten die Produktinnovationen sowie Vertriebsaktivitäten finanzieren zu können
Logistikprinzip, in dem der Kunde das Produkt beim Lieferanten oder der vorgelagerten Bearbeitungsstufe holt/holen lässt und dadurch dessen Nachproduktion initiiert. Das Produkt wird quasi durch die Produktion gezogen
Logistikprinzip, in dem die Aufträge von der Fertigungssteuerung anhand eines zuvor geplanten Produktionsprogrammes freigegeben und durch die Produktion geschoben werden
Darstellen der Ist-Qualifikation von Mitarbeitern für direkte, indirekte und selbssteuernde Tätigkeiten und Definieren der künftigen Qualifikationen in übersichtlicher Form
Methode, um Prozesse in ihren Strukturen, Bestandteilen und Daten zu analysieren, darzustellen und zu bewerten. Sie lässt sich auf der Ebene des Arbeitsplatzes, des Produktionsbereichs oder der gesamten Fabrik erstellen
Weiterentwicklung der Kostenvergleichs- und Gewinnvergleichsrechnung. Hier fließt das sog. ökonomische Prinzip mit ein, indem der Kapitaleinsatz zusätzlich einbezogen wird. Ergebnis ist die durchschnittliche jährliche Verzinsung des Kapitals, das für die Investition eingesetzt wird, oft auch als Return On Invest (ROI) bezeichnet. Man setzt dieses Verfahren ein, um verschiedene Investitionsvarianten in Bezug auf die Rendite miteinander zu vergleichen oder auch bei Einzelinvestitionen, um eine Mindestverzinsung zu realisieren
Wenige A-Produkte repräsentieren bis zu 70 % der Effekte. Optimierungsprojekte werden i. d. R. nicht für alle produzierten, sondern lediglich z. B. für die A-Produkte durchgeführt (vgl. ABC-Analyse). Durch diese Beschränkung werden der Planungsaufwand und die Planungszeit erheblich reduziert
Methode, um Verluste innerhalb maschineller Bearbeitungsprozesse oder beim Personal zu eliminieren oder zu reduzieren, indem die durchzuführenden Tätigkeiten während des Rüstprozesses analysiert und optimiert werden
Visuelle Darstellung einer Transportmatrix, in der die Hauptmaterialflüsse möglicht mittig mit dicken Pfeilen und die Nebenmaterialflüsse mit dünnen Pfeilen dargestellt werden. Es sind erste Hinweise auf die materialflussgerechte Anordnung von Arbeitssystemen ableitbar
Zeichnerische Grundrisse und mit Pinnadeln aufgesteckte, verschiebbare Flächenelemente bzw. Magnetfolien, die auf den Grundrissen haften. Vorteile: betroffene Mitarbeiter können aktiv in die Planung einbezogen werden; es ist keine Software notwendig
Ein Auftragseinsteuerungspunkt im Gesamtprozess, der für alle anderen Prozesse den Produktionsrhythmus vorgibt. Dabei wird flussaufwärts nach dem Pull-Prinzip und flussabwärts nach dem Push-Prinzip verfahren
Tätigkeiten, die sich auf Managementaspekte beziehen, wie An-/Abwesenheitsplanung, Qualifizierungsplanung, KVP oder die Pflege von Informationstafeln/-wänden
Eigenschaften von Zielen: Speziell (konkret, auf viele Bereiche übertragbar, nicht zu viele Ziele: max. zwei je Dimension), Messbar, Anforderungsgerecht (stimmig mit der Vision/den Unternehmensgrundsätzen, für alle nachvollziehbar), Realistisch (voll beeinflussbar, reproduzierbar, geringer Erhebungsaufwand), Termingerecht (monatliche, wöchentliche oder tägliche Aktualisierung und Abrufbarkeit)
Werkzeugwechsel im einstelligen Minutenbereich. SMED steht für: Single Minute Exchange of Die. Es geht vor allem darum, Verschwendung zu identifizieren und zu reduzieren, um z. B. im Arbeitssytem (Maschine) mehr Varianten fertigen zu können
Art und Weise, wie z. B. eine Vision, Unternehmensgrungsätze oder Unternehmensziele erreicht werden. Eine Strategie kann z. B. ein Balanced Scorecard-System sein
Struktur, die sich unterscheidet in die Phasen 1) Analyse (Datenaufnahme und Bewertung) und 2) Gestaltung
Methode, um die Sicht von Mitarbeitern in Bezug auf die Unternehmensumwelt in Form von Chancen (Opportunities) und Risken (Threats) sowie in Bezug auf das Unternehmen selbst mittels der Stärken (Strengths) und Schwächen (Weaknesses) kennenzulernen
Struktur, die auf dem Modell des Arbeitssystems basiert. Hier geht es im Besonderen um die drei Systemelemente Arbeitsgegenstand, Betriebsmittel und Mensch
Methode, um miteinander gekoppelte Arbeitssysteme dahingehend zu überprüfen, ob deren Zyklus- oder Prozesszeiten unter oder über dem Kundentakt liegen. Ziel ist es, den Taktausgleich zu minimieren und den Bandwirkungsgrad zu maximieren
Methode zur autonomen Instandhaltung (durch Betriebsmittelbediener), zur verbeugenden Instandhaltung und zum Controlling der Instandhaltungskosten
Basis zur Erstellung einer Transportmatrix. Sie wird in Paletten/Jahr, Gitterboxen/Jahr oder z. B. Mitarbeitertransporte/Jahr angegeben. Es ist zu beachten, dass die Mitarbeiterkosten i. d. R. die absolut bestimmende Größe für den Transportkostensatz darstellen. Im Vergleich zum Fördermittel machen sie nicht selten 80 % der Gesamtkosten aus. Es sollten somit die Mitarbeiterbewegungen erfasst werden. Meist wird die Transporteinheit mit einer Mitarbeiterbewegung korrelieren, etwa wenn eine Palette von einem Fördermittel transportiert wird, das ein Mitarbeiter bedient
Methode, in der in einer Matrixdarstellung (von/nach) die Transportintensitäten zwischen Arbeitsysstemen dargestellt werden. Meist werden die Transporteinheiten pro Jahr aufgeführt
Untersuchung des Unternehmensumfelds, das nicht oder kaum beeinflussbar ist, wie die gesamt-ökonomische Situation, Branchen, Märkte, Kunden oder Wettbewerber
Optimierung bestehender Layouts, Arbeitssysteme usw. mit i. d. R. vorhandenen Planungseinschränkungen
Grundsätze, die eher auf den Unternehmenszweck gerichtet sind; z. T. stellen sie auch Verhaltensgrundsätze nach innen und nach außen dar. Sie dienen der Verbindung von Vision und Unternehmenszielen und sind mittelfristig (3-5 Jahre) angelegt
Operationalisierung der Vision und der Unternehmensgrundsätze. Sie sind auf Kurzfristigkeit (1 Jahr) angelegt. Unternehmensziele sollten sich an den Dimensionen einer Balanced Scorecard orientieren
Bereitstellen und Verwalten von Ressourcen, damit die Funktion der Geschäfts-/Kernprozesse sichergestellt ist. Sie sind damit quasi als ‘interner Dienstleister’ zu betrachten und werden durch interne Kunden-Lieferanten-Beziehungen gekennzeichnet. In Unterstützungsprozessen agieren i. d. R. indirekte Funtionsbereiche, in denen indirekte Tätigkeiten erfolgen
Überflüssige Tätigkeiten, Prozesse, Abläufe, Zeiten, Materialien, Stillstandszeiten, Kosten usw., die im Rahmen von Prozessoptimierungsvorhaben mit höchster Priorität beseitigt werden sollten
Methode, mit der umfangreiche Arbeitsabläufe, wie z. B. Rüstwechsel, aufgenommen und im Nachhinein analysiert werden können. Die Aufnahmen können beliebig oft angesehen werden, Zeitdauern von Sequenzen lassen sich direkt ablesen und durch die Wiedergabe in Zeitlupe (slow motion) ist es möglich, komplexe Bewegungsabläufe nachzuvollziehen. Zudem werden betriebliche Abläufe nicht gestört
Wesentliche Aussagen zur langfristigen Ausrichtung (5-10 Jahre) eines Unternehmens. Auf einer Vision basieren Unternehmensgrundsätze und Unternehmensziele. In diesem Zusammenhang wird auch oft von Unternehmensphilosophie gesprochen
Methode, die auch als Spaghetti-Diagramm bezeichnet wird, um Wege eines Mitarbeiters oder Produkts zu visualisieren. Die Methode wird meist im Rahmen der REFA-Arbeitsablaufanalyse, der Rüstanalyse oder von 5S (5S-Check) eingesetzt
Methode, in der in einer Matrixdarstellung (von/nach) die Entfernungen zwischen Arbeitsysstemen dargestellt werden. Es werden nur dort Werte in die Wegematrix eingetragen, wo dies auch in der Transportmatrix erfolgt ist, denn nur die Wege sind relevant
Standardisiertes, physisch vorhandenes Mittel (auch Software) zur Anwendung und Umsetzung von Methoden. Beispielsweise unterstützt das Werkzeug Shadowboard (Schattenbrett) die Methode 5S
Sämtliche Tätigkeiten, die den Wert eines Produktes bzw. einer Dienstleistung für den Kunden erhöhen, z. B. maschinelles Bearbeiten oder Montieren
Schnelle und wenig aufwändige Aufnahme von Ist-Prozessen mit definierten Parametern (z. B. Bestände, Bearbeitungszeiten, Zykluszeiten, Durchlaufzeiten), um sich einen groben Überblick zu verschaffen. Ziel ist es, Verschwendung und deren Ursachen zu identifizieren, diese mit Kennzahlen zu bewerten, gezielt Gestaltungsmaßnahmen nach Richtlinien zu erarbeiten und einen Umsetzungsplan zu erstellen
Verhältnis aus Durchlaufzeit und gesamter Bearbeitungszeit
Statisches Verfahren für Investitionsvorhaben, wie sie im Fokus dieses Buches stehen. Dabei kommen meist zur Anwendung: Kostenvergleichs-, Gewinnvergleichs-, Rentabilitäts- und Amortisationsrechnung
Methode, um die zeitliche Verteilung/Schwankung von Artikeln anhand ihrer Verbrauchsstruktur mit den drei Segmenten X, Y, Z darzustellen
Zeit, in der ein Teil in einem Arbeitssystem fertig produziert wird. Die Zykluszeit kann durch eine Erhöhung von Ressourcen (Mitarbeiter oder Betriebsmittel) reduziert werden
Checkliste, mit der der 5S-Status in Arbeitssystemen erhoben und nach umgesetzten Maßnahmen überprüft und dokumentiert werden kann. 5S wird in folgender Reihenfolge umgesetzt: 1. Sortiere aus, 2. Systematieren, 3. Sauber halten, 4. Standardisieren, 5. Selbstdisziplin